Prefabricated Houses, also known as prefab or modular houses, are a construction method where building components are prefabricated in factories and then transported to the construction site for assembly. Compared to traditional cast-in-place concrete buildings, the construction cycle of prefabricated houses is significantly shortened. This construction method benefits from the following key factors:
1. Factory Production and Standardized Operations
The core of prefabricated houses lies in “prefabrication,” where building components are produced in the factory according to uniform standards. Factory production offers the following advantages:
Standardized Operations: The factory uses an assembly line production method, with clear operating procedures and standards for each step, reducing uncertainties in the construction process. Workers repeatedly operate at fixed stations, improving skill levels and greatly increasing production efficiency.
High Mechanization: Factories are equipped with advanced machinery such as automated cutting machines and welding robots, enabling fast production of components while avoiding errors and inefficiencies in manual operation.
Controlled Environment: Factory production is not affected by weather, temperature, or other external environmental factors, allowing continuous operation and ensuring production continuity and stability.
2. Parallel Construction, Shortening Construction Period
Traditional construction usually follows a linear process, proceeding sequentially through foundation, main structure, and interior finishing, where each step waits for the previous to complete before starting. Prefabricated house construction adopts a parallel process:
Factory and site work simultaneously: While components are produced in the factory, foundation treatment, and basic site work can proceed on-site. Once components are transported to the site, they are assembled directly, greatly shortening the overall construction period.
Modular Assembly: Prefabricated houses usually use modular design, with most finishing and equipment installation completed in the factory. On-site work only involves connecting the modules together. This “plug-and-play” approach significantly reduces on-site construction time.
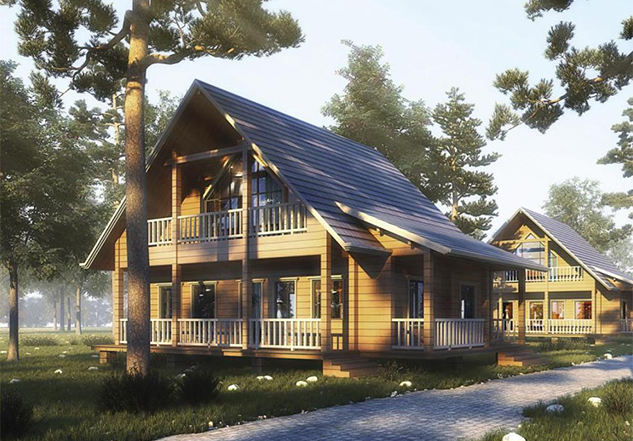
3. Reducing On-Site Construction Steps
Traditional construction requires a large amount of wet work on-site, such as concrete pouring and wall masonry. These steps are not only time-consuming but also easily affected by weather and material supply. Prefabricated house construction greatly reduces on-site construction steps:
Direct installation of prefabricated components: Walls, floors, roofs, and other components are prefabricated in the factory, and on-site work only involves hoisting and fixing, eliminating the curing time required for cast-in-place concrete.
Predominantly dry work: Construction mainly uses dry processes such as bolting and welding, reducing on-site wet work like cement and mortar, avoiding delays caused by wet operations.
4. Quality Control and Improved Construction Efficiency
Factory production of prefabricated houses not only improves construction efficiency but also significantly enhances building quality:
Strict quality control: The stable factory environment allows rigorous quality inspection at every step of component production, ensuring precision and strength. In contrast, quality control on traditional construction sites is more difficult and prone to errors.
Reduced rework: Since most processing and inspection are completed in the factory, the probability of problems during on-site assembly is greatly reduced, minimizing rework and construction delays caused by quality issues.
The content of this article is sourced from the internet; if there are any issues, please contact me for removal!
Leave a Reply