We must not overlook the welding technology of modular panel booth, as it is the key to long-term use. Its stability and sealing performance need to be promptly mastered, and the welding technology of the booth manufacturer directly affects its stability and sealing. Here are several important points regarding the welding technology of modular panel booths.
When the material thickness of the modular panel booth exceeds a certain limit, a V-shaped groove must be made before welding to ensure full penetration. During the welding process of the booth, high temperatures may cause oxidation that can damage the oxide layer. At this time, rust prevention must be extensively applied, and multi-layer or multi-pass welding should be used, following a specific welding sequence.
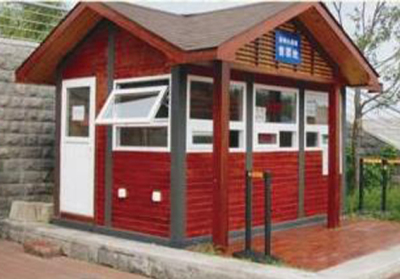
When performing multi-layer welding, smaller diameter welding rods can be selected. The choice depends on the diameter, length, and gap of the rods. It is important to ensure full penetration at the root during welding. If the welding materials contain impurities, galvanic corrosion may occur, accelerating corrosion. Therefore, slag must be thoroughly cleaned before welding, and the weld density should not be too high.
Excessive weld density can damage the original mechanical structure and reduce the load-bearing capacity to some extent. After welding, the surface of each weld bead must be flat, with slight concavity on both sides, avoiding convexity or undercutting. The welding process of the bottom layer of the modular panel booth must be handled carefully. During welding, it is necessary not only to ensure fusion on both sides but also that the weld height does not exceed the steel plate surface.
The content of this article is sourced from the internet; if there are any issues, please contact me for removal!
Leave a Reply