As the craze for self-built houses in rural areas continues to heat up, more and more families face a key decision when building their homes: stick with the traditional brick-and-mortar structure or try the emerging light steel structure villas?
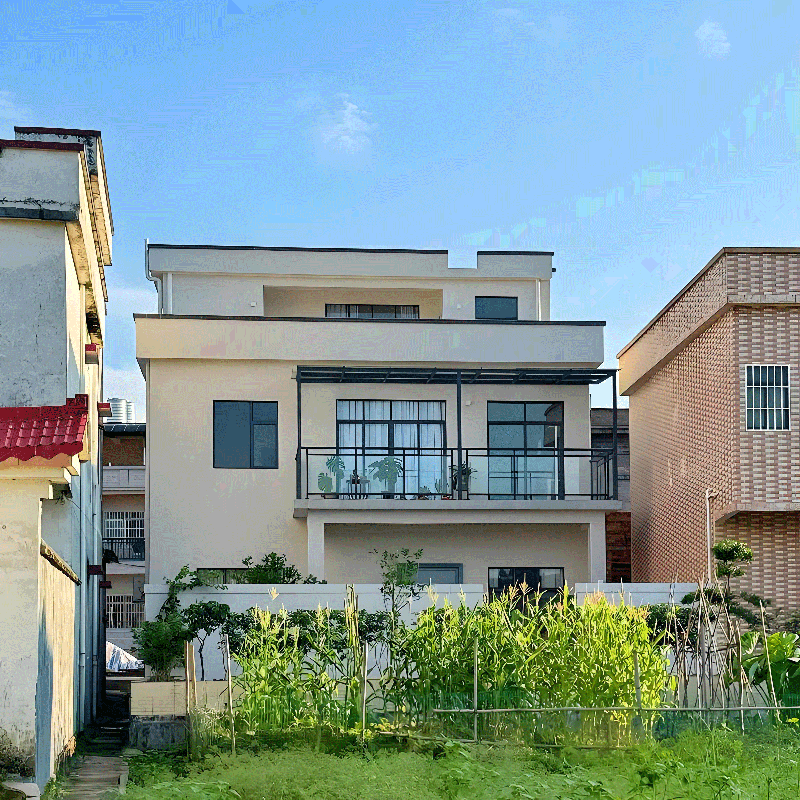
New Trend in Rural Housing: Light Steel Villas VS Traditional Brick-Concrete – How to Choose Without Getting a Bad Deal?
In cold regions such as Liaoning, Jilin, and Heilongjiang, light steel houses are gradually gaining popularity. They are widely used in rural homes, villas, guesthouses, and scenic area accommodations. This article analyzes the pros and cons of these two construction methods from the perspectives of structural safety, construction period, cost, living comfort, and more, to help you make an informed choice.
1. Structural Safety: Light Steel Structures Are More Resistant to Earthquakes and Wind
Light steel villas use galvanized light steel keel as the main structure with scientifically designed joints, offering strong integrity and excellent earthquake and wind resistance. Data shows they can withstand magnitude 8 earthquakes and level 12 typhoons, suitable for most rural and even remote mountainous areas.
Brick-concrete structures rely on masonry bearing walls and have poorer seismic performance, especially if foundations are unstable or construction is unregulated. Rural construction is often manual with inconsistent standards.
Conclusion: Light steel structures outperform brick-concrete in structural safety.
2. Construction Period & Seasonal Adaptability: Light Steel Is Faster
Aspect | Light Steel Villa | Traditional Brick-Concrete |
---|---|---|
Construction Time | 30-45 days | 90-180 days |
Seasonal Impact | Can be built year-round (factory prefabrication) | Winter stoppage, rain delays |
Light steel structures are prefabricated in factories and assembled onsite, ensuring high standardization and fast construction with fewer human errors.
Traditional brick-concrete involves multiple steps, relies heavily on weather and manual labor, resulting in longer and more variable timelines.
Conclusion: Light steel construction is much faster than traditional brick-concrete.
3. Construction Cost: Similar Total Cost, Light Steel More Transparent
Rural buyers often worry if light steel houses are expensive. Here’s a cost comparison:
Structure Type | Average Cost (CNY/m²) | Notes |
---|---|---|
Brick-Concrete | 800 – 1500 | Excludes design, decoration, maintenance |
Light Steel Villa | 1000 – 1800 | Includes structure, insulation, wiring, facade design |
Light steel may cost slightly more per square meter but includes insulation, windows, electrical wiring, reducing secondary construction later. Fast construction and lower labor costs also make overall investment more manageable.
Conclusion: Costs are comparable, but light steel offers more transparency and standardization.
4. Comfort & Energy Efficiency: Light Steel Has Clear Advantages
- Insulation: Walls integrate insulation layers (EPS/XPS boards, fiberglass), keeping warmth in winter and cool in summer—ideal for Northeast China.
- Sound & Thermal Insulation: Multi-layer wall construction performs better than brick masonry.
- Energy Saving: Saves 50%-60% energy, meeting national green building standards.
- Ventilation: Thoughtful design allows active ventilation, preventing dampness and mold.
Traditional brick-concrete homes often suffer from cold winters, hot summers, and poor ventilation.
Conclusion: Light steel houses offer superior comfort and energy efficiency.
5. Policy & Future Trends: National Support for Prefabricated Buildings
Since the 13th Five-Year Plan, China’s Ministry of Housing and Urban-Rural Development has promoted prefabricated buildings. During the 14th Five-Year period, light steel and prefab houses are widely included in government pilot and subsidy programs.
Rural construction policies are shifting toward “green, energy-saving, modular, and lightweight” methods. Traditional outdated techniques may face restrictions. Light steel structures are prioritized in new rural construction and rural revitalization projects.
Conclusion: Policy direction favors light steel as the future mainstream for rural housing.
6. Suitable Use Cases: Which Structure Fits Whom?
Suitable For | Recommended Structure | Reason |
---|---|---|
Rural first-time self-build, long-term living | Light Steel Structure | Better insulation and durability |
Fast construction, limited budget | Light Steel (simple single-story) | Shorter construction time, can build in stages |
Traditional craftsmanship lovers, skeptical of new materials | Brick-Concrete | Better psychological acceptance |
Scenic area guesthouses, mobile housing | Light Steel / Modular | Modular advantages |
Cold, windy regions | Light Steel Structure | Better earthquake and wind resistance |
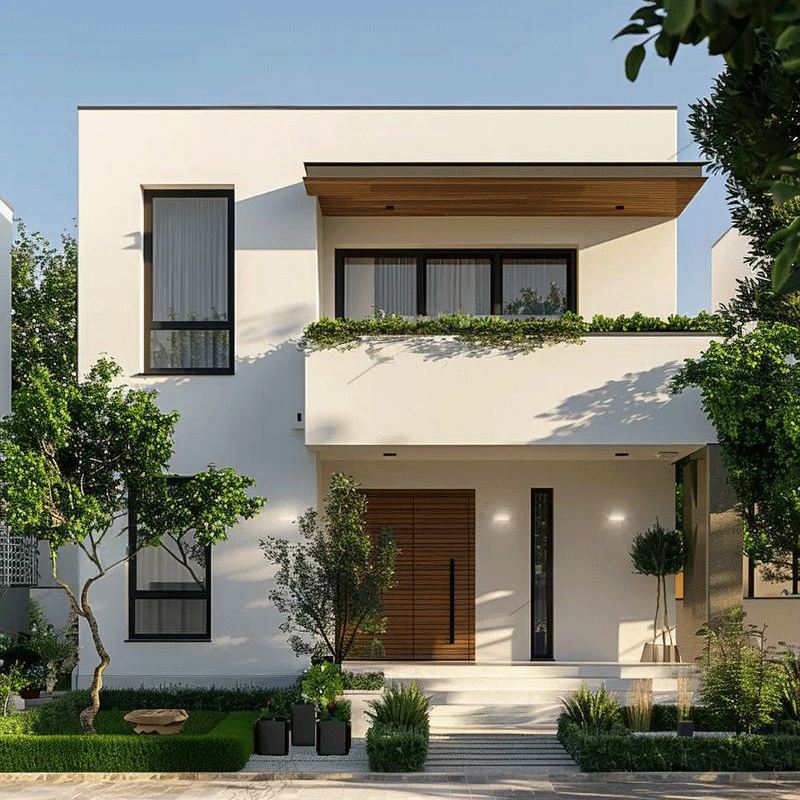
Summary: Choose Light Steel Structures to Save Money and Worry Less
Overall, light steel villas outperform traditional brick-and-mortar houses in structural safety, construction speed, living comfort, and energy efficiency. Coupled with strong government support, especially in cold regions like Northeast China and Inner Mongolia, light steel houses are gradually becoming the new trend for rural homebuilding.
If you’re planning to build a home, a guesthouse, or a new house for your parents, it’s worth seriously considering light steel structures — they may be more reliable, economical, and convenient than you expect.
Want to learn more about custom designs, construction processes, and pricing for light steel homes? Contact us for personalized one-on-one rural homebuilding solutions.
Leave a Reply