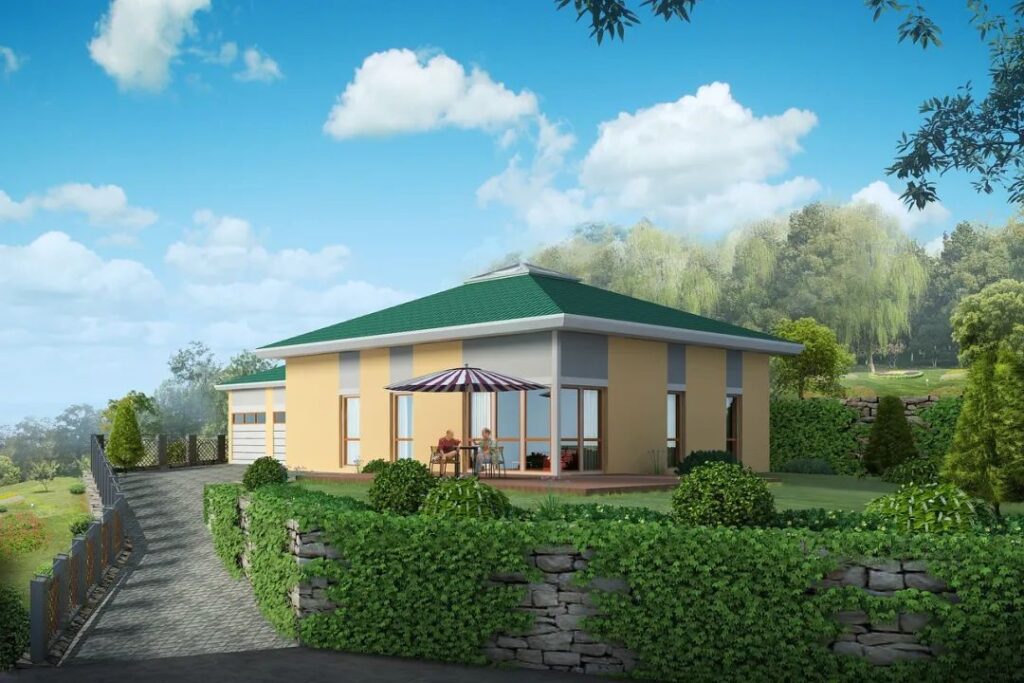
In recent years, prefabricated buildings have frequently become a hot topic in the construction industry, with many regions successively introducing policies to encourage the development of prefabricated construction. Prefabricated buildings have already been implemented in many areas and are no longer far from our daily lives.
Prefabricated building
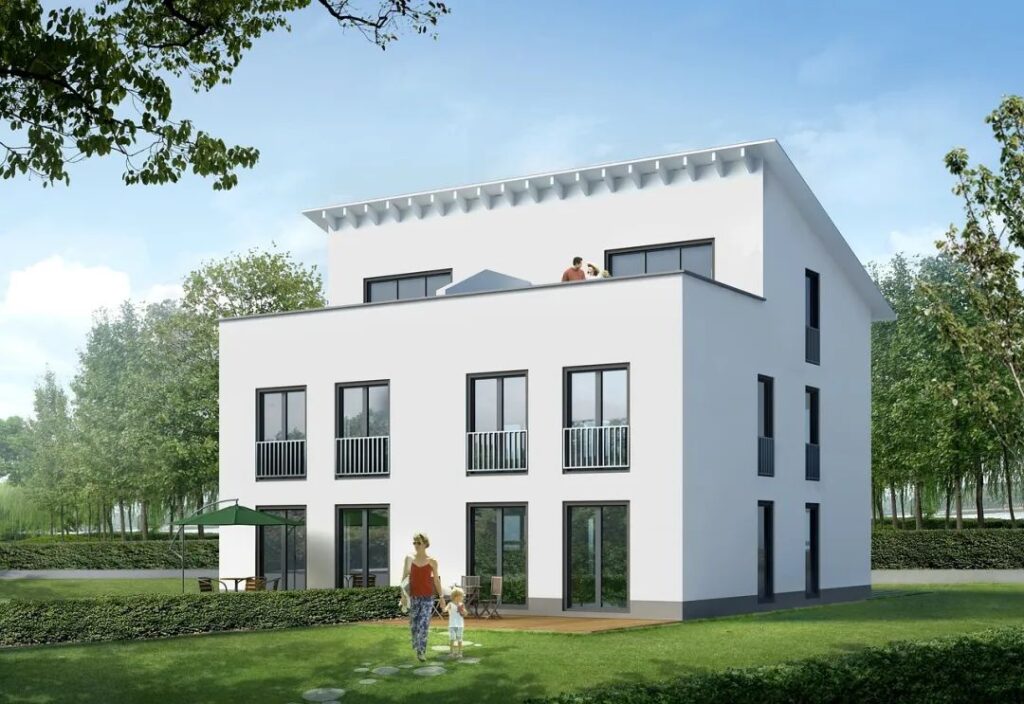
What is prefabricated building?
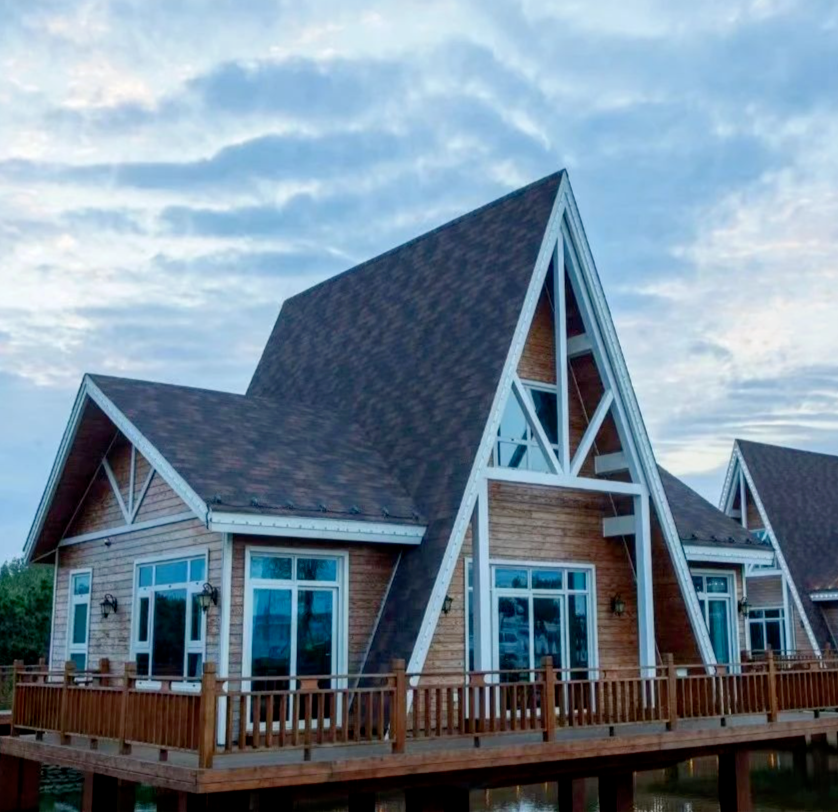
Prefabricated building refers to a construction method that shifts a large portion of on-site work to the factory. Building components and parts—such as floor slabs, wall panels, stairs, balconies, etc.—are manufactured in the factory, then transported to the construction site where they are assembled and installed through reliable connection methods.
Prefabricated buildings mainly include precast concrete structures, steel structures, and modern timber structures. Because they adopt standardized design, factory production, assembly construction, information management, and intelligent applications, they represent a modern industrialized production approach.
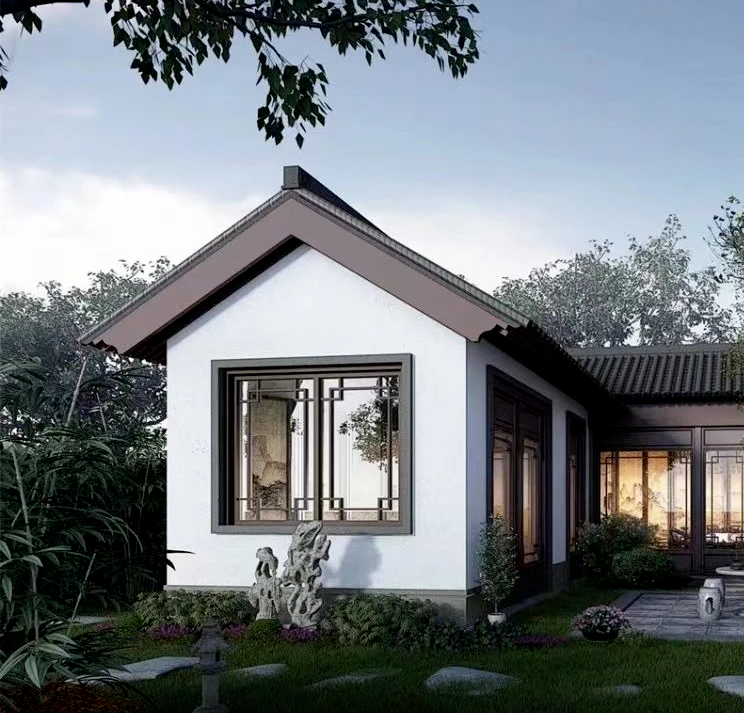

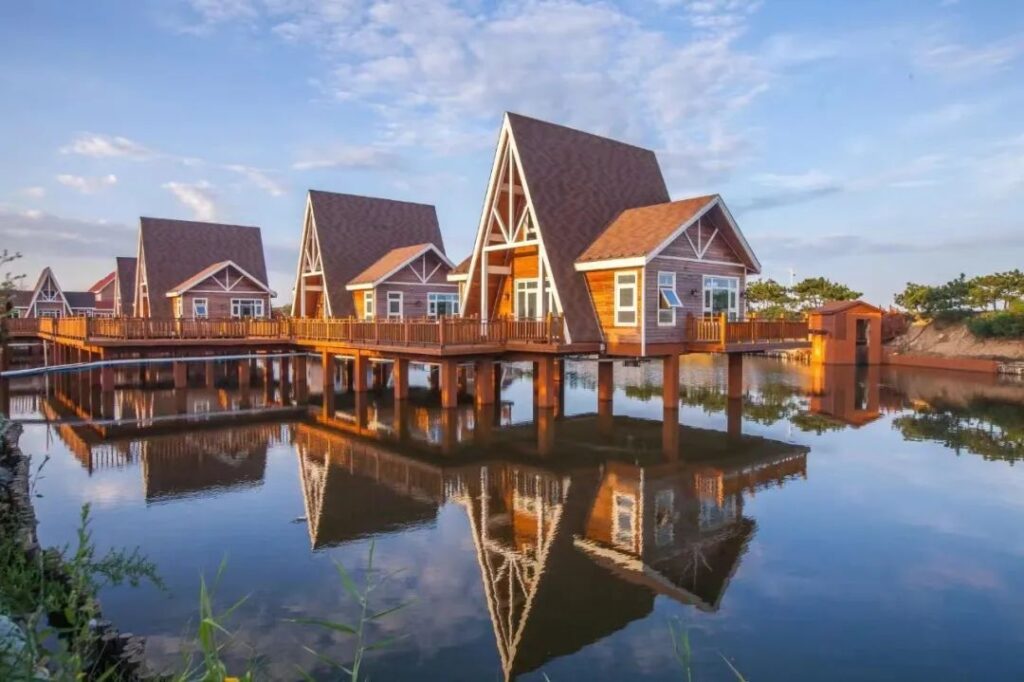
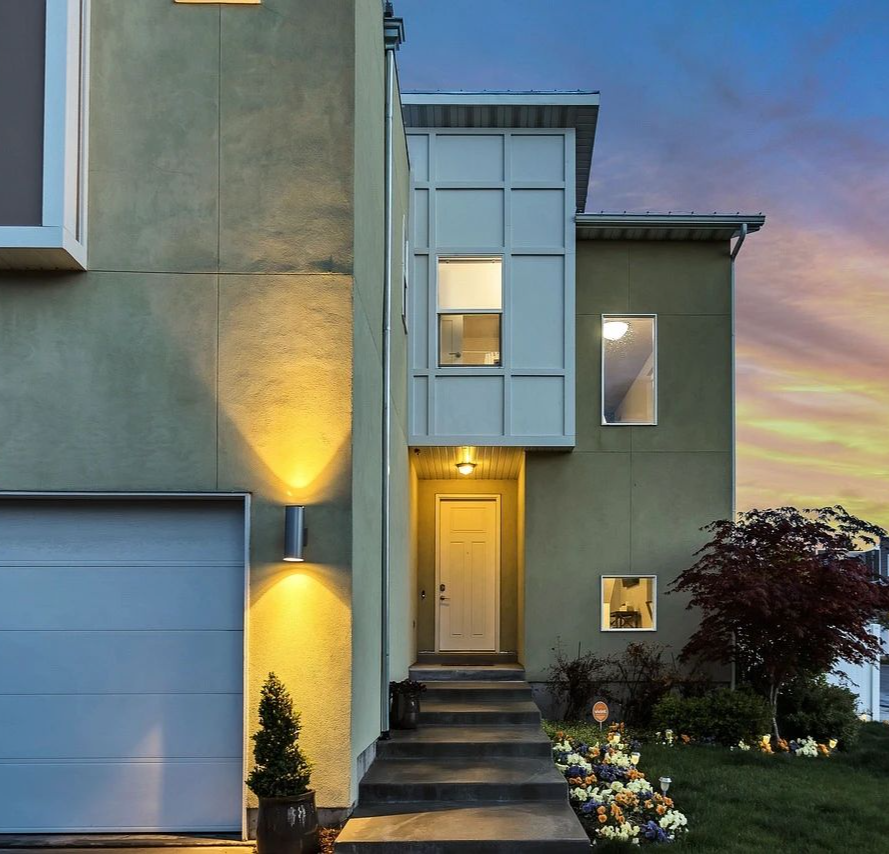
Prefabricated building
Why is prefabricated construction being widely developed?
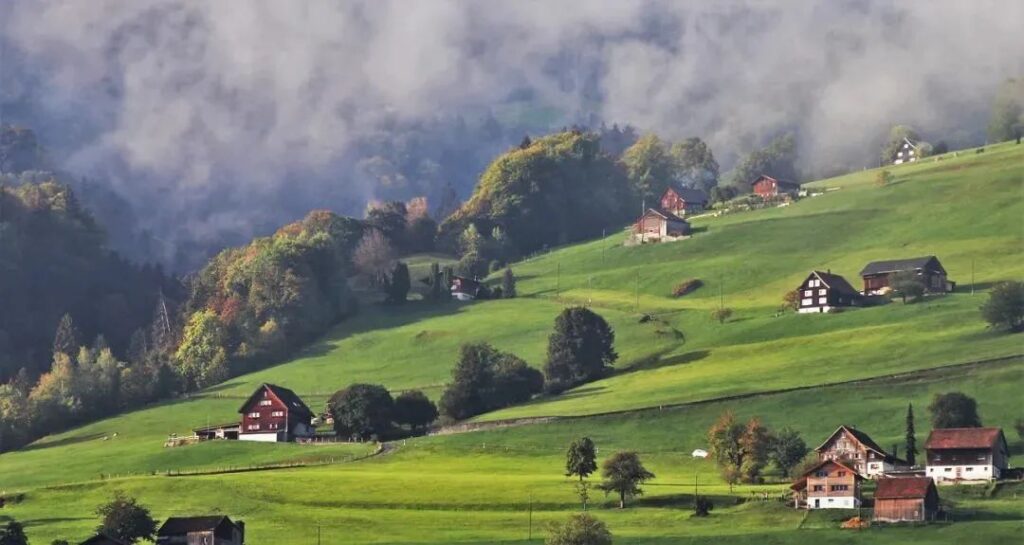
(1) National Policy Promotion
The Ministry of Housing and Urban-Rural Development and the National Development and Reform Commission issued the “Notice on the Implementation Plan for Carbon Peak in Urban and Rural Construction,” which proposes advancing green and low-carbon construction.
The notice emphasizes vigorously developing prefabricated buildings and promoting steel-structured housing. By 2030, prefabricated buildings are expected to account for 40% of new urban construction annually.
(2) Requirements for the Transformation and Upgrading of the Construction Industry
The common on-site casting (or masonry) construction method widely used in China’s construction industry generates a large amount of waste and causes air and noise pollution. The excessively extensive production methods lead to resource waste.
To better improve the urban environment and promote ecological civilization, adhering to a sustainable development path, the transformation and upgrading of the construction industry is urgent. Developing prefabricated buildings aligns with the current needs of industry development.
Many engineers feel that traditional civil engineering is “falling behind.” In fact, the construction industry is facing significant challenges in industrial upgrading as its growth slows. Developing prefabricated buildings is timely and necessary.
A new industry will emerge
Developing prefabricated buildings will create market demand and capital flow for component manufacturing, specialized equipment production, information technology, and logistics industries, promoting industrial development and increasing employment. Moreover, as the industry deepens, it will drive the growth of many supporting industries.
Prefabricated
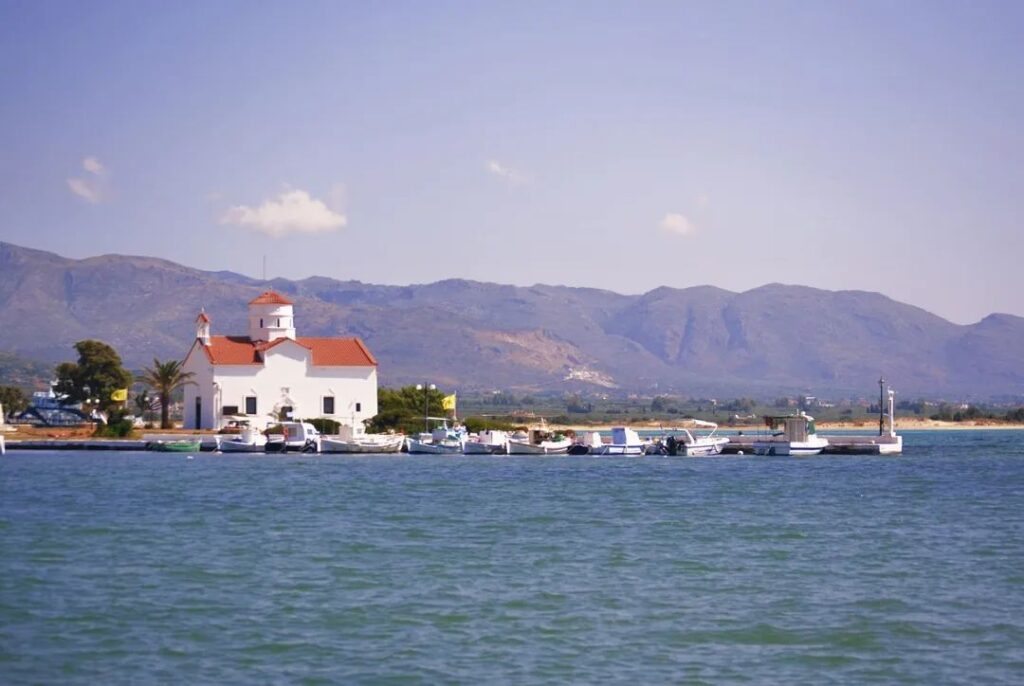
(3) Higher Requirements for Building Quality
With urbanization and population growth, housing has become a major concern, and there are higher demands for the performance and quality of residential buildings. The industrialized model of prefabricated buildings has greater advantages in building quality, construction speed, and environmental protection and energy efficiency.
Driving Economic Development
Based on the development experience of pilot cities for national residential industrial modernization, introducing “a batch of enterprises,” building “a batch of projects,” and driving “a region” has formed “a series of new economic growth points.” The development of prefabricated buildings effectively promotes rapid regional economic growth.
(4) Rising Labor Costs
Many construction sites now face a “labor shortage.” The scarcity of skilled workers and low labor efficiency are major constraints on the development of the construction industry.
Transforming production methods can effectively ease the labor shortage, improve production efficiency, and comprehensively advance the modernization level of the construction industry.
Leave a Reply