1. Overview of Prefabricated Buildings
Prefabricated buildings refer to buildings whose parts or entire components are prefabricated in factories, then transported to the construction site and assembled through reliable connection methods. Compared with traditional cast-in-place buildings, prefabricated buildings have significant advantages such as faster construction speed, stable quality, energy saving, and environmental protection. In recent years, with strong national policy support and the demand for transformation and upgrading in the construction industry, prefabricated buildings have developed rapidly in China.
In the field of residential self-built houses, prefabricated buildings are gradually changing the traditional housing model with their unique advantages. Data shows that in 2022, the proportion of newly started prefabricated buildings nationwide reached about 25%, with the proportion of steel structure prefabricated buildings increasing year by year, especially showing great strength in the rural self-built housing market.
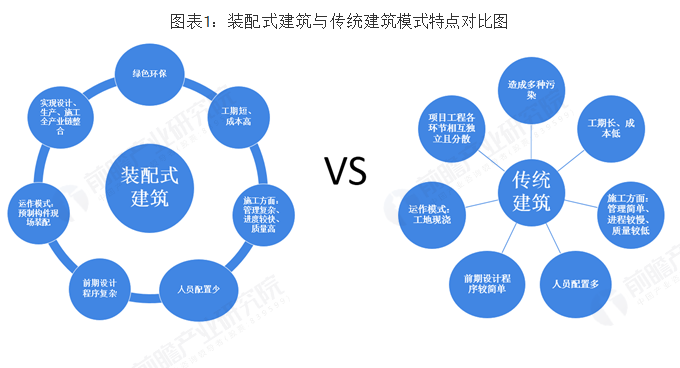
Comparison Chart of Prefabricated and Traditional Construction Methods
2. Material Selection and Technical Features
- Cold-formed Thin-walled Light Steel Structure
Cold-formed thin-walled light steel structure is currently one of the most popular forms of prefabricated buildings in residential self-built houses. This system uses hot-dip galvanized steel plates with a thickness of 0.6-2.0mm, cold-formed into C-shaped, U-shaped, and other cross-section components, which are connected by self-tapping screws to form walls, floors, and roof systems.
Technical features:
① Lightweight, about 1/5 to 1/8 of traditional brick-concrete structures; fast construction speed, with a 200㎡ house main structure completed within 7-10 days.
② Excellent seismic performance, able to resist earthquakes of magnitude 9; flexible space layout, convenient for later renovation.
Energy-saving and environmentally friendly.
③ Dry construction process, reducing construction waste.
④ Suitable for 1-3 story low-rise residential buildings, villas, homestays, tourist vacation houses, especially suitable for earthquake-prone areas and regions with poor geological conditions. - Heavy Steel Structure
Heavy steel structure self-built houses mainly use H-shaped steel, square steel pipes, and other main load-bearing components, combined with lightweight floor slabs and enclosure systems to form a complete building system. Compared with light steel structures, heavy steel structures have larger span capacity and load-bearing capacity.
Technical features:
① High structural strength, suitable for large-span space design.
② Good durability, with a design service life of over 50 years.
③ Better fire resistance than light steel structures.
④ Modular design achievable, with high factory prefabrication degree.
⑤ Suitable for 3-6 story multi-story residences, large space villas, and self-built houses requiring special functional spaces.
Based on the above material standards and features, and according to our company’s years of construction experience, we believe using light steel keel steel structure as the main body is more suitable for the current market demand.
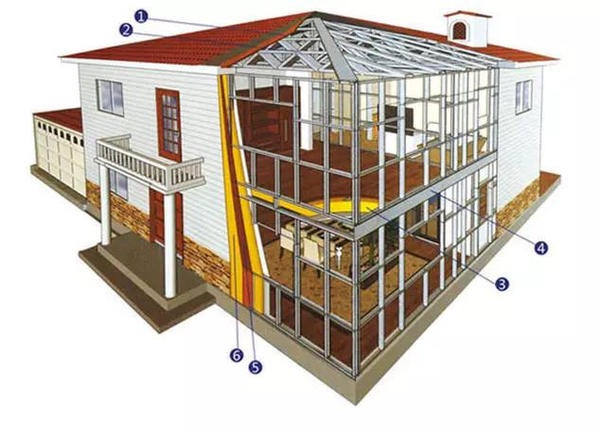
Reasons for Recommendation:
Outstanding economy: cost about 1500-2500 RMB/㎡, basically equal to traditional brick-concrete structures, but with higher overall benefits.
Convenient construction: no need for large construction machinery, basically unaffected by seasons, can be constructed normally in winter.
Stable quality: high precision of factory prefabrication, avoiding quality fluctuations caused by manual construction.
Energy-saving and environmentally friendly: walls can be filled with insulation materials, with overall insulation performance more than three times that of brick-concrete structures.
Policy support: many local governments provide area rewards or subsidies for self-built houses using prefabricated buildings.
3. Market Prospects Analysis
Strong market demand
With the promotion of rural revitalization strategy and the increase of rural residents’ income levels, the residential self-built housing market is undergoing a transition from “having a house to live in” to “living in a good house.” Traditional brick-concrete houses no longer meet the new era’s requirements in terms of comfort, seismic resistance, and design flexibility.
Policy dividends continue to release
National-level continuous supportive policies create a favorable environment for the development of prefabricated buildings in the self-built housing field: The “14th Five-Year Plan for the Development of the Construction Industry” clearly requires that by 2025, the proportion of prefabricated buildings in new constructions should reach over 30%. Many provinces and cities provide financial subsidies of 100-300 RMB per square meter for rural prefabricated houses, and some pilot areas simplify the approval process for prefabricated self-built houses, shortening approval time.
Mature industrial chain
After years of development, China’s prefabricated building industry chain has basically matured: the number of professional design and construction teams has rapidly increased, the supporting material supply system is sound, costs have gradually decreased, industry standards and regulations have been continuously improved, quality assurance systems have been established, and consumer awareness has improved. With the increase of demonstration projects and media promotion, consumers’ acceptance of prefabricated buildings has significantly increased. Data shows awareness rose from less than 30% in 2018 to 65% in 2022. Satisfaction surveys indicate that prefabricated house owners have a satisfaction rate of 89%, higher than traditional buildings, with main focus gradually shifting from price to quality, comfort, and personalized design.
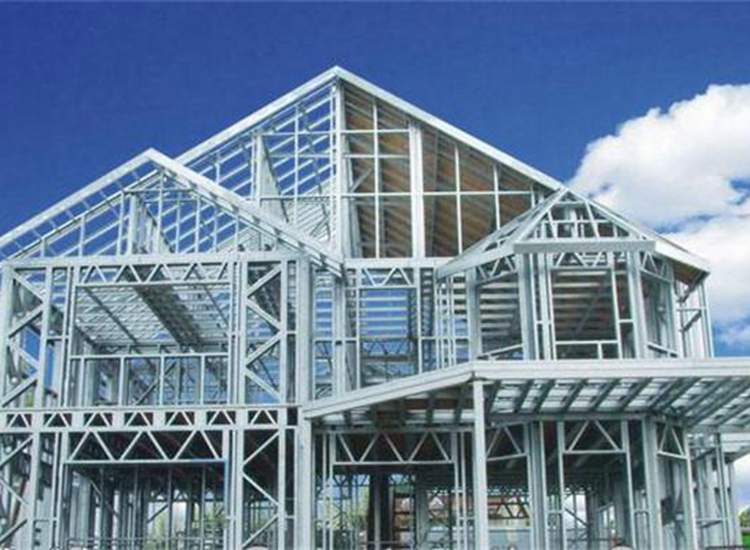
4. Development Suggestions and Outlook
- Although the prospects are broad, the full promotion of prefabricated buildings in the residential self-built housing market still faces some challenges:
- Strengthen publicity and promotion: through demonstration projects, VR experiences, and other means, eliminate consumers’ misunderstandings of “tin houses.”
- Improve the standard system: formulate technical standards and acceptance specifications suitable for rural areas to ensure quality and safety.
- Train professional teams: strengthen construction personnel training to solve the “last mile” installation service problem.
- Innovate financial support: develop special loan products for prefabricated self-built houses to reduce initial investment pressure.
- Promote personalized customization: develop modular design software to meet diverse and personalized consumer needs.
Looking ahead, with technological progress and consumption upgrades, it is expected that by 2025, the penetration rate of prefabricated buildings in the self-built housing market will exceed 20%, especially with greater development space in the following fields:
- Rural tourism supporting facilities (homestays, vacation houses, etc.)
- Reconstruction projects in earthquake-prone areas
- Characteristic town construction
- Emergency shelter housing
- Eco-friendly demonstration zones
Prefabricated buildings are not only a transformation in construction methods but also an important path to promote high-quality development of the construction industry and achieve the “dual carbon” goals. In the residential self-built housing market, it represents a greener, more comfortable, and safer future living direction, with promising development prospects.
Author: Liaoning Rundong New Materials Technology Co., Ltd.
Pan Peigang
June 15, 2025
Leave a Reply