“Living and working in peace and contentment” has been a simple yet profound wish of the Chinese people since ancient times, reflecting the deep connection between rural homes and cherished memories. However, the construction quality and safety of self-built houses are often difficult to guarantee.
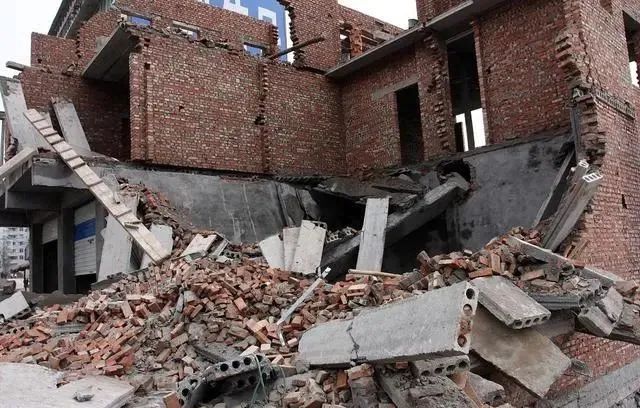
Data shows that since 2000, there have been more than 20 publicly reported self-built housing accidents in China, resulting in over 110 deaths, with most of the collapsed rural houses being brick-concrete structures.
In fact, in most countries, detached houses are also self-built, just like in rural China.
The difference is that brick-concrete structures are still widely used here, and traditional housing construction often suffers from issues such as lack of design blueprints, unregulated construction practices, and inconsistent material quality. Most homes are built without proper design — some simply imitate the appearance of neighbors’ houses, some follow the basic sketches of construction foremen, and some design their own homes without professional knowledge, leading to various quality and safety issues.
Alternatively, people may purchase house plans but hire unqualified local teams to build them, resulting in houses that look completely different from the original design.
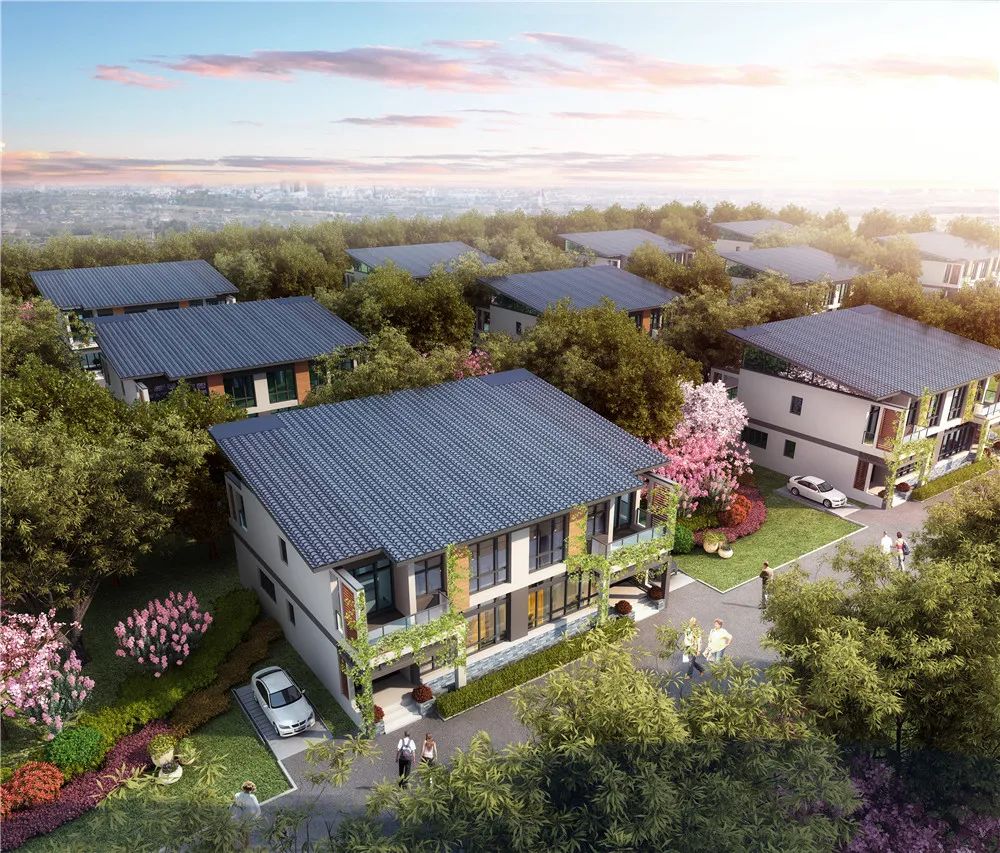
In many foreign countries, prefabricated housing has already become the mainstream for rural home construction. Prefabricated building materials replace traditional red bricks, and intelligent construction methods replace on-site wet operations, significantly reducing construction time. These homes also offer remarkable advantages in terms of environmental protection, energy efficiency, safety, and comfort.
Despite the many benefits of prefabricated buildings, in China, they are mainly applied to urban high-rise projects and have not yet brought widespread housing upgrades to rural communities.
Today, let’s take a closer look at prefabricated homes, with the hope that this information will help those planning to build a house.
01
What is a prefabricated house?
Unlike traditional brick houses, which require manual laying of bricks and mixing of cement — a process that is time-consuming, labor-intensive, environmentally unfriendly, with uncontrollable costs and inconsistent quality — prefabricated houses are built using factory-made components and parts.
These components include beams, columns, floor slabs, interior and exterior wall panels, staircases, connection nodes, plumbing, electrical systems, etc. They are transported to the construction site and assembled using reliable connection methods to form the complete building.
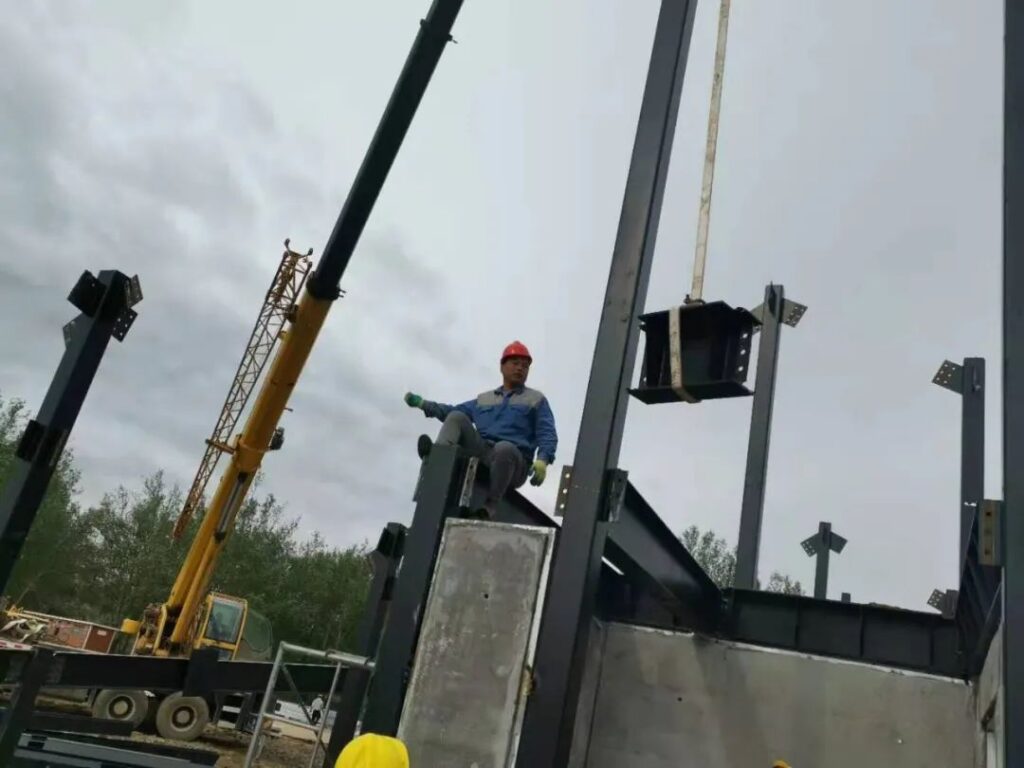
Prefabricated housing eliminates the complicated manual construction processes involved in traditional building methods, providing better control over both construction costs and quality.
02
Are prefabricated homes safe?
The components of prefabricated buildings are manufactured in factories using modern production equipment and strict processes, ensuring precise fabrication and controlled quality. Compared to traditional on-site manual construction, factory-based production offers better dimensional accuracy, material quality, and overall performance of the components, effectively enhancing the overall safety of the building.
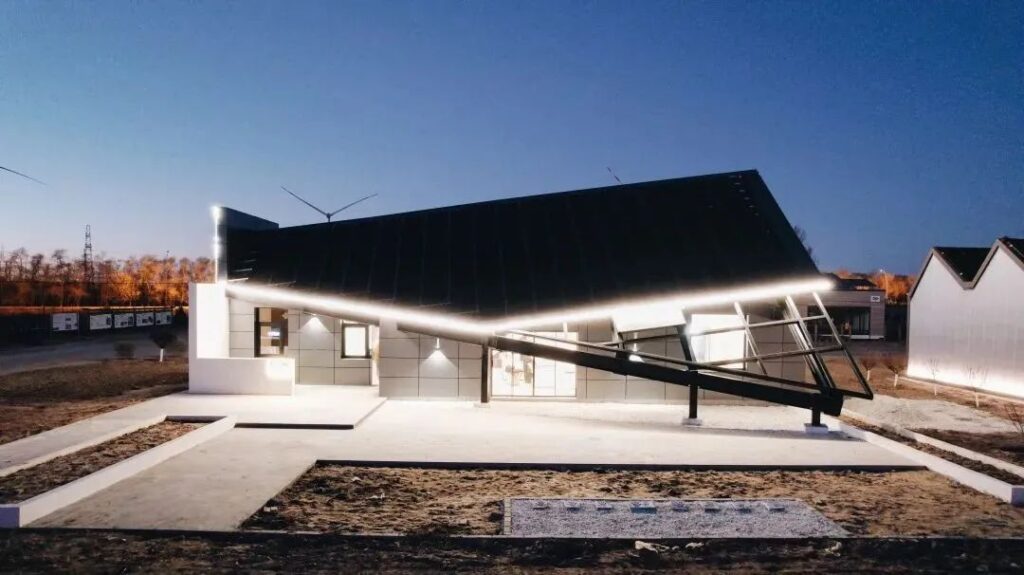
Prefabricated buildings use factory-made components for assembly-based construction. The connections between components typically adopt methods such as reinforced steel connections, welding, or bolt fastening. These connection methods undergo strict design and testing to ensure the overall structural stability and seismic performance.
In addition, the structural load-bearing capacity and deformation resistance are fully considered during the design and construction process of prefabricated buildings, ensuring that the structure can maintain good stability and safety when subjected to external forces.
Therefore, ordinary homebuyers can confidently purchase prefabricated homes without worrying about their safety.
03
Do prefabricated houses have other advantages?
In addition to the convenience and speed of construction, as well as structural safety and earthquake resistance mentioned above, Hanergy Green Building’s independently developed polystyrene particle mortar-filled walls also offer many advantages, such as being lightweight yet high-strength, providing thermal insulation, keeping interiors warm in winter and cool in summer, and offering sound insulation and noise reduction.
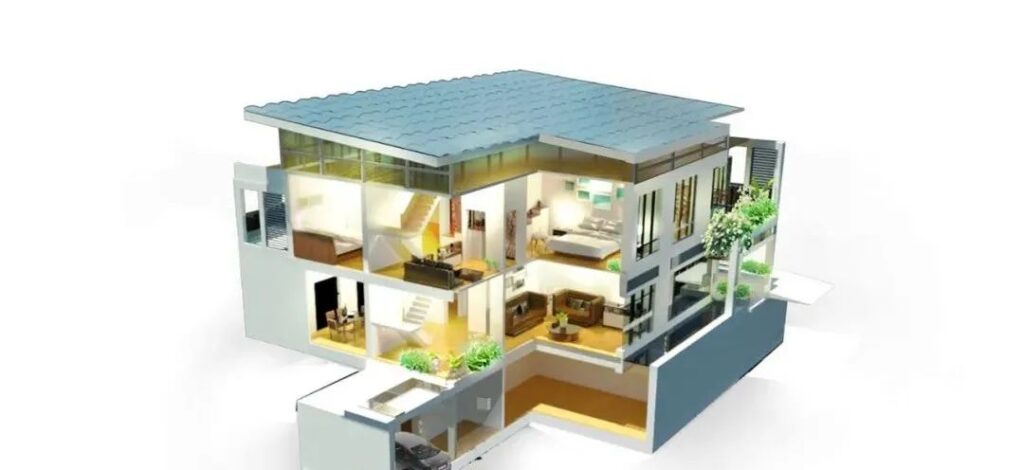
04
Can prefabricated houses be recycled?
Traditional rural brick houses are almost always a one-time build; once completed, they cannot be dismantled or easily modified, making the construction process nearly irreversible. In contrast, one major advantage of prefabricated houses is their recyclability and reusability. They can be disassembled and reassembled later. If relocation or resale is needed, prefabricated houses offer much greater flexibility and significantly lower costs compared to traditional brick houses, which usually have to be demolished and rebuilt.
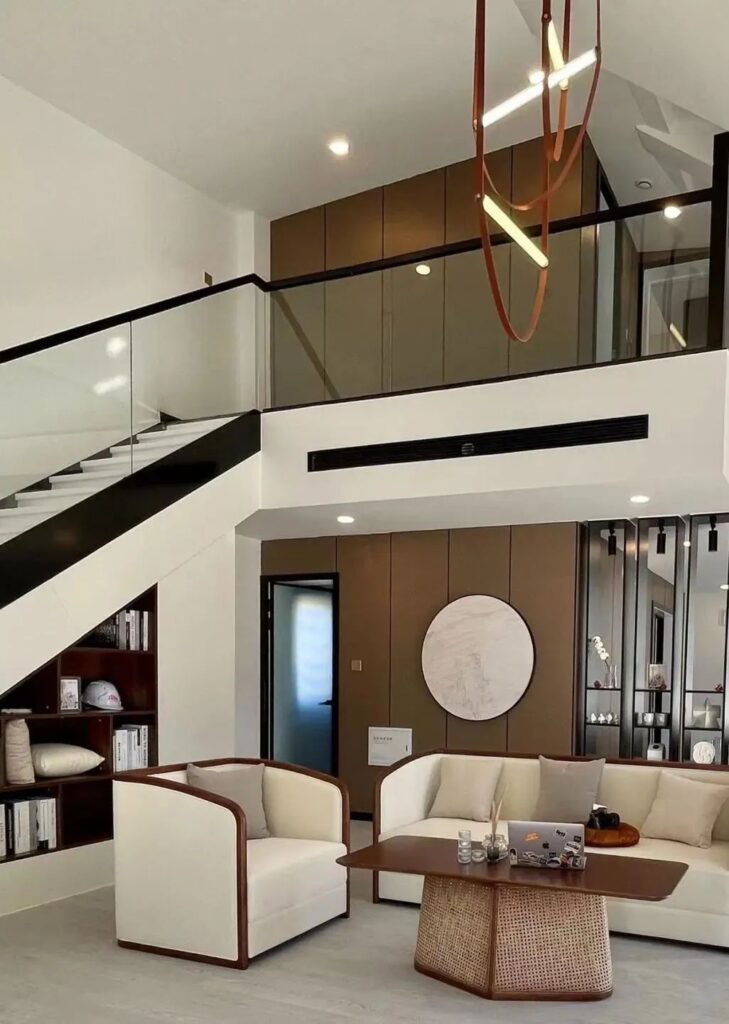
In China, “falling leaves return to their roots” is more than just an idiom;
it reflects countless people’s deep affection and longing for their hometown.
Building a house back home is often a lifelong must.
In recent years, with the government’s strong promotion of fully prefabricated buildings and various local subsidy policies, prefabricated rural villas have become increasingly recognized and chosen.
What exactly are their advantages? Are they worth building?
Through the answers to the ten questions above, we believe you have formed your own judgment.
If you plan to build a rural villa, it’s worth exploring further.
Leave a Reply